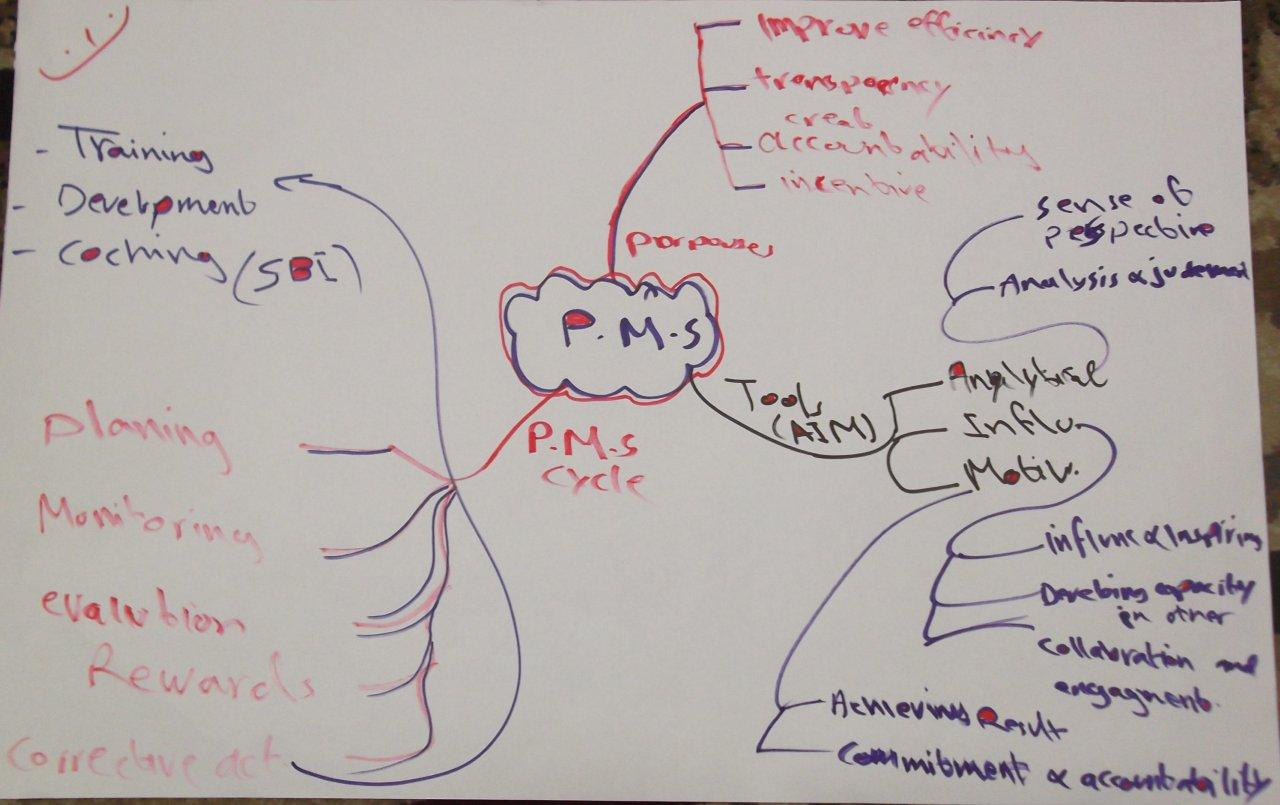
The leverage to the secret of contextual thinking is that the more you build trust in the existing managerial paradigm...
The leverage to the secret of contextual thinking is that the more you build trust in the existing managerial paradigm...
At some point in our life, some of us may have experienced a person who helped us to see our...
Here are some typical Questions and our Answers regarding the deployment of Lean Six Sigma in an organisation. If you...
Not every organisation needs to develop process managers with Lean and Six Sigma skills. Yet, every organisation deserves to have...
A few years ago I was leading a session for high potential managers in an international phone company. Before I...
Two weeks after joining Central Bank in Germany, I spend a full week in the so-called Black Belt Training by...
Thinking ahead is a cardinal rule of business. In addition to monitoring the daily operations of your business, succession planning...
A team spends months on improving customer-facing branch processes of a bank. After benchmarking with sister companies across the world...
Becoming a Black Belt is not for everyone. More important than statistical knowledge are personal traits and some leadership characteristics....
Every year around December, he gets very busy. He plans for the big event and he wants to make sure...
There are several invaluable lessons learnt during the different phases of YOG. A significant task has been the recruitment, preparation...
I was chatting with a friend of mine who is in a senior leadership position. He wanted to implement a...
Discussing workforce planning with an HR professional of a government entity in Singapore we explained our approach that starts from...
Imagine you join a new kind of job in a different line of business you don’t have any experience in....
Especially in service organisations, productivity is usually quite low due to a lack of efficiency caused by a missing focus...
Copyright © 2025 by COE Pte Ltd. All Rights Reserved.