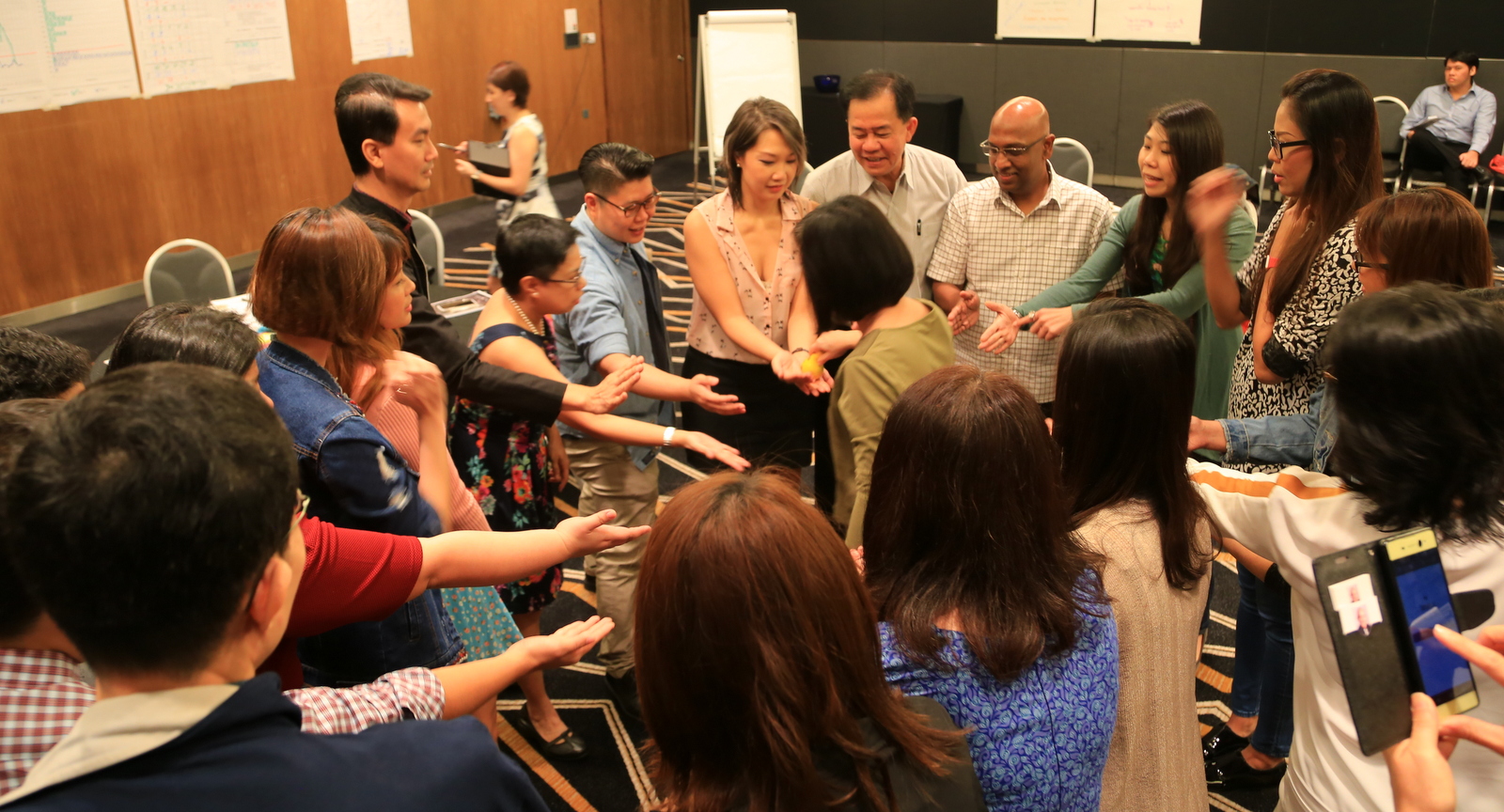
Lean Government. Even to the seasoned Lean practitioner, this idea sounds far-fetched. Governments are traditionally seen as the epitome of...
Lean Government. Even to the seasoned Lean practitioner, this idea sounds far-fetched. Governments are traditionally seen as the epitome of...
Do You Like Spaghetti? About unnecessary motion and other lean sins “I did a lot of spaghetti walk this morning”,...
MYTH: LEAN SIX SIGMA HAS MANY TOOLS I DO NOT NEED. Certainly, life is much easier without the need to...
Combining Lean Six Sigma (LSS) with a thorough analysis of your Working Capital Situation can lead to a more objective...
Leaders need to spend more time at the real touch points impacting customers and employees. Only then will they truly...
Lean application outside of the manufacturing sector is frequently met with scepticism. Oft cited reasons are that service providers do...
Here are some typical Questions and our Answers regarding the deployment of Lean Six Sigma in an organisation. If you...
Everyone, undoubtedly, has had the unenviable honour of experiencing ‘bureaucratic government processes.’ Be it applying for your first ID or...
An Australian construction equipment rental & leasing firm had decided to implement an Enterprise Resource Planning system in 12 months....
After a Lean programme for inventory was instituted the production facility struggled with getting a good product mix out to...
Today, organisations must change their priorities from a traditional focus on planning and control to emphasising speed, innovation, flexibility, quality,...
Copyright © 2025 by COE Pte Ltd. All Rights Reserved.