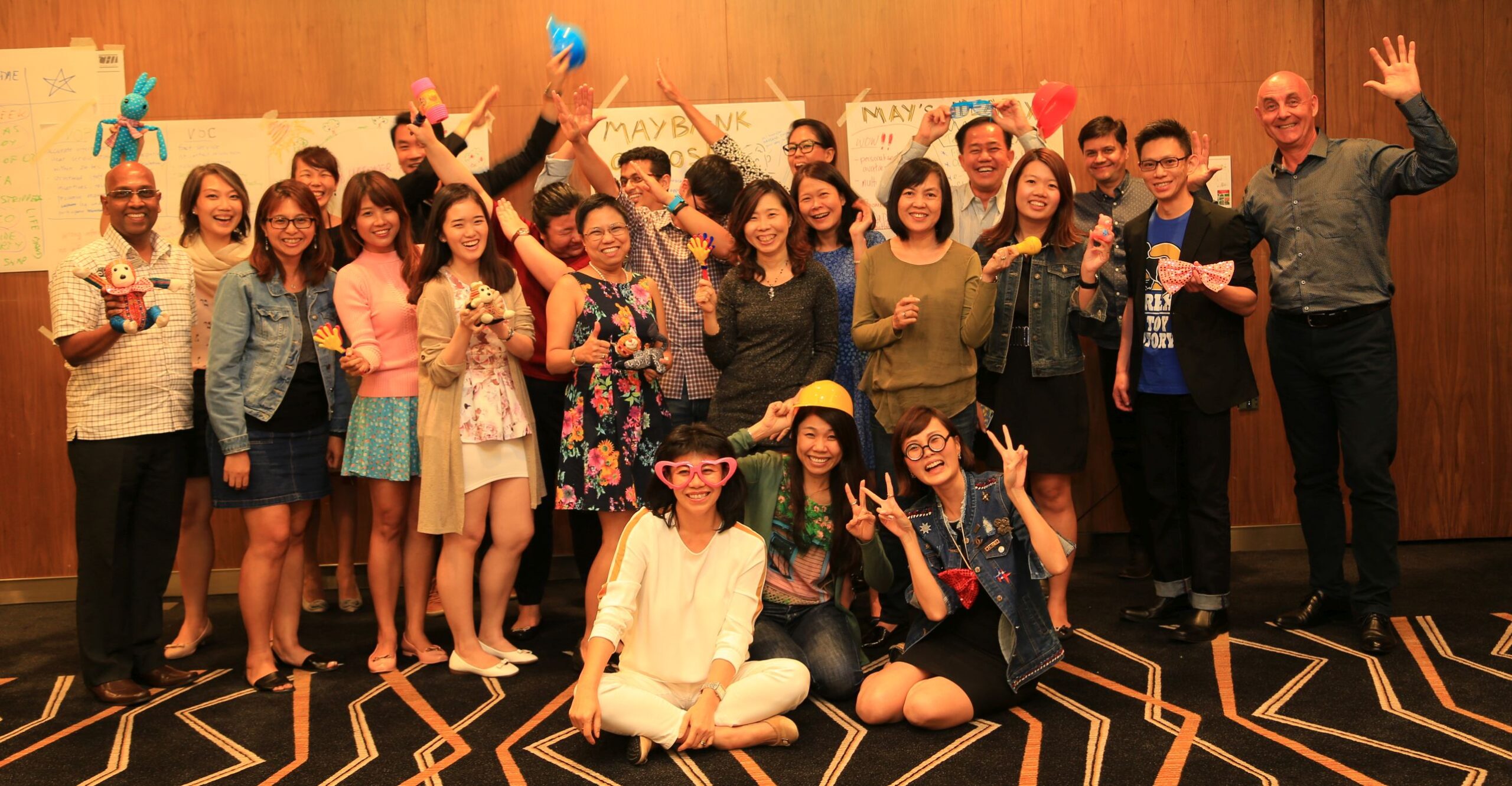
Innovation has drawn tremendous attention in the business world over the last decades and seems to be up on the...
Innovation has drawn tremendous attention in the business world over the last decades and seems to be up on the...
“We have great news for you. Our project is delivering results already.” The team is all smiles when they give...
Have you ever considered how much unnecessary paper you receive from banks, you immediately feed into the bin? Rethinking the...
Leaders need to spend more time at the real touch points impacting customers and employees. Only then will they truly...
Project selection for improvement is taken rather seriously. Some companies have even developed highly sophisticated methods for to ensure project...
Over the last decade, companies and organisations in nearly every industry all over the world have introduced Lean Six Sigma...
Here are some typical Questions and our Answers regarding the deployment of Lean Six Sigma in an organisation. If you...
Not every organisation needs to develop process managers with Lean and Six Sigma skills. Yet, every organisation deserves to have...
I was chatting with a friend of mine who is in a senior leadership position. He wanted to implement a...
Besides business and functional know-how, a successful leader must have competencies in leading change and improving, designing and managing processes....
Some time ago, I was facilitating a Six Sigma project group involved in solving a process challenge. This group had...
New undertakings or experiences are always challenging at first. This is no different when Schenker Singapore (Pte) Ltd, a transportation...
The job of purchasing is obviously to source for reliable suppliers who deliver products conforming to specification on time within...
“Don’t use Six Sigma to tackle special cause variation!” is one of the common phrases being repeated by Lean Six...
Against the common belief, statistical knowledge is not a criterion for selecting your Belts. However, the capability to acquire new...
Copyright © 2025 by COE Pte Ltd. All Rights Reserved.