Here are some typical Questions and our Answers regarding the Lean Six Sigma deployment in an organisation. If you have more questions, please feel free to add them as a comment and we will try to answer.
Q: Where does Lean Six Sigma come from?
Lean Six Sigma is not a “slim version” of Six Sigma. It is rather a combination of two powerful methodologies. Lean has been developed mainly by Toyota over the last 40+ years. Six Sigma is a result of Motorola’s work to improve the quality of their TV production line from 1985 to 1988.
Q: What is the difference between Lean and Six Sigma?
Lean focuses on reduction of waste with the main idea of getting rid of non-value-added steps in any kind of process. Six Sigma focuses on reducing the variation in processes that are really needed. Only combined can these two methodologies with their powerful tool sets achieve the best impact.
Q: Which company can apply Lean Six Sigma?
It is hard to answer this question because there is rarely an organisation that has no room for improvement. The wide application of this powerful approach speaks for itself. There is always use for an application of modern methods to close performance gaps. Whether these gaps and the environment need a customised approach and not the full suite of tools is something that needs to be decided case by case.
Q: How do we start a Lean Six Sigma deployment?
One of the most important tasks for the senior management is to explain why your organisation needs this. It is additional work for many people and they may not like the idea without understanding the need for a Lean Six Sigma deployment. Create a shared need!
Then, you should look for some projects that will definitely help the organisation and that will definitely succeed. Run these as pilots, use them to gain more buy-in and develop some belts on the way.
Before you start, make sure you do an excellent job in defining these projects.
Q: Who will be involved?
The senior management has the important job of explaining the “burning platform” at the outset, overseeing selection of projects and belts at the beginning, keeping the people involved motivated and guided along the way as well as challenging and monitoring results. If senior management is not committed, do not start a Lean Six Sigma deployment!
Sponsors are members of the management team who want to have their process “fixed”, have gaps closed and performance improved. They are usually attached to one or a few projects as the management representative. They usually do not sit in team meeting but join at important junctures.
Black Belts and Green Belts are the project leaders. They have full responsibility for leading the team, application of tools, communicating with the sponsor, addressing issues and delivering results.
Team members are part of the project team in order to make sure that the team as sufficient knowledge and experience with the whole process to be improved.
Master Black Belts are internal or external coaches who are usually necessary in the first phase of deployment when belts and sponsors are inexperienced with the new approach.
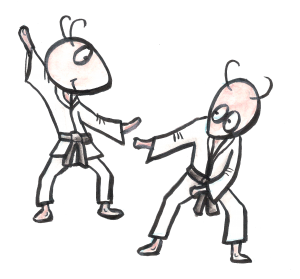
Green Belts or Black Belts are the Project Leaders for Lean Six Sigma Projects
Q: How much time do Lean Six Sigma teams spend on their project?
This is hard to say. A rule of thumb is: over a period of 4 to 6 month they should spend some hours to half a day, i.e. up to 10% on the project related work. During some periods, they will probably need more time due to voice of the customer collection or due to data gathering. Sometimes it is definitely less.
Q: Do we need to give the people involved some training?
Definitely yes. Black Belts and Green Belts will need to handle a multitude of new tasks involving new tools. They certainly need to be trained otherwise they can not perform the task. Green Belts usually receive up to 12 days of training – spread over a period of about 2 to 3 months. Black Belts are Green Belts with project experience and additional training of another up to 10 days.
Some sponsors think they do not need. Wrong. Over the course of the project they will recognise that their teams speak a language they do not understand. They then ask for training. Two to four days is a good start.
Even the teams deserve some basic introduction. A day could be a good start and a nice support for the work of the Green Belt.
Q: Who should be a Black or Green Belt?
For both of them, similar criteria apply: They are from lower to middle management levels, belong to your talent pool and are planned for a significant promotion mid-term. They have some leadership competencies like ability to drive change cross-functional, coaching skills, communication skills, ability to prioritise to the benefit of the company, project management skills and a great enthusiasm. And, they need some basic analytical skills enabling them to learn and run powerful analysis tools.
Q: What is a “good Lean Six Sigma project”?
- A good project is starting with a “pain” that is measurable. Something like “Customers complain about the turn-around-time between submitting an application for a loan and receiving the decision.”
- A good project has an objective, which is often only put in place after getting some data about the problem. A SMART objective would look like “Reduce the turn-around-time for small consumer loans from currently 92% above 2 days to 90% below one day until end of August.”
- A good project has a sponsor who wants this problem fixed, a Black or Green Belt who has a stake in it and a team who is able to cover the process from beginning to end.
However, I have not seen many “perfect projects”.
Q: How do we “find” these projects?
There are plenty of sources highlighting process issues. These are customer complaints or feedback, employee complaints or suggestions, process issues seen in your KPI or dashboard system, your balanced scorecard or even your financials. Even things that do not look like process issues such as “Large Accounts Receivables” stem from some kind of process upstream. Even “lack of knowledge” of some frontline officers shows that either the recruitment process or the training and development process or the appraisal process hide some gaps.
If someone tells me that his company has no Lean Six Sigma project candidates, I would either conclude that he is not very serious about his business or he can not see the flow of his business in the process perspective.
Q: Are there other approaches apart from Lean Six Sigma focussing on process excellence?
Yes, definitely. There are other approaches that can complement or substitute LSS. Lean Six Sigma focuses on mainly common cause variation, i.e. variation that is immanent of the process. It is rather weak when it comes to fire-fighting. Unfortunately, we need fire-fighting sometimes. Kepner Tregoe or PSDM is the better choice for this. I do not really like to recommend something like TQM. I have never seen one clear definition of what it comprises. LSS is very structured, very rigid, very driven and therefore it will certainly deliver results.
Q: Why should someone be interested in participating as a Green Belt if this is that much additional burden?
On the other hand, many high-level leaders in companies like GE have been developed out of the pool of successful Black Belts or Master Black Belts.
Q: Is Lean Six Sigma similar to ISO 9000 or any of the Quality Awards like MBQA, EQA, SQC/SQA etc?
No, it is not. It is rather complementing them. The above mentioned frameworks show requirements an organisation has to fulfill if they want to achieve high customer satisfaction, process efficiency and staff motivation. These frameworks say, WHAT needs to be done. Lean Six Sigma has tools to fulfill the requirements. It answers many HOW questions by showing the way. For example, ISO9000 requires the organisation to make sure that representative measurements are collected in a repeatable and reproducible manner. LSS has Gage R&R to fill this gap with a very powerful approach.
Q: Is there any Innovation in LSS solutions?
Actually, this depends. LSS does offer creativity techniques to come up with more creative solutions if needed. It is a matter of how the project is scoped, how the team is led by sponsor and belt as well as how the tools are being trained. We will certainly work with Creative Problem Solving (CPS, Buffalo) tools when it comes to solutioning.
Q: What can go wrong during a Lean Six Sigma Deployment?
There are some drivers for success of a Lean Six Sigma deployment: As usual, firstly, the senior management must believe in it. Otherwise, it will most likely fail. Secondly, it is key to involve the right people. Selecting the HiPos sends the signal that this is important to the management. Thirdly, recognition and rewards should be part of the plan. This could involve even considering promotion for those who make it – consistently. Lastly, selecting the right projects that help solving company issues is a major driver for success. There are some more that only become important when the aforementioned are in place.