Power up your Lean Six Sigma training with Innovation tools and get to results faster. Try Lean Innovation Training (LIT).
What is Wrong with the Traditional LSS Training?
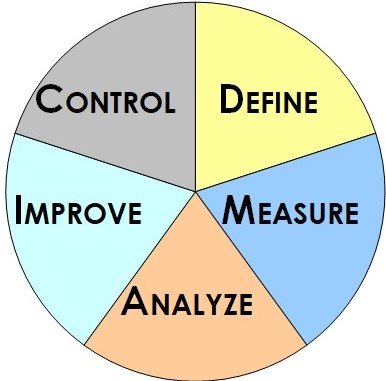
As a result, combining the customer-oriented Lean Six Sigma (LSS) toolbox with innovation-driving Creative Problem Solving (CPS) tools in a shorter Lean Innovation Training (LIT) has the potential to overcome the apparent short-comings of the former (Lameijer et al., 2021). We kept the proven DMAIC cycle, as this rigid roadmap is one of the great achievements of LSS.
How Does Lean Innovation Training (LIT) Work?
Our Lean Innovation Training (LIT) consists of four training sessions with coaching in between (see figure). The first session spreads over two days and will (a) teach a solid set of tools, (b) select projects for applying these tools and (c) inspire people to participate.
This session, the introduction workshop, is open to all management and staff and aims to give an overview of the methodology through an experiential business simulation game. This exercise creates opportunities for participants to learn hands-on and transfer this learning into own business situations by identifying opportunities for improvement and innovation. By the end of this workshop, a list of potential LIT projects would have been established.
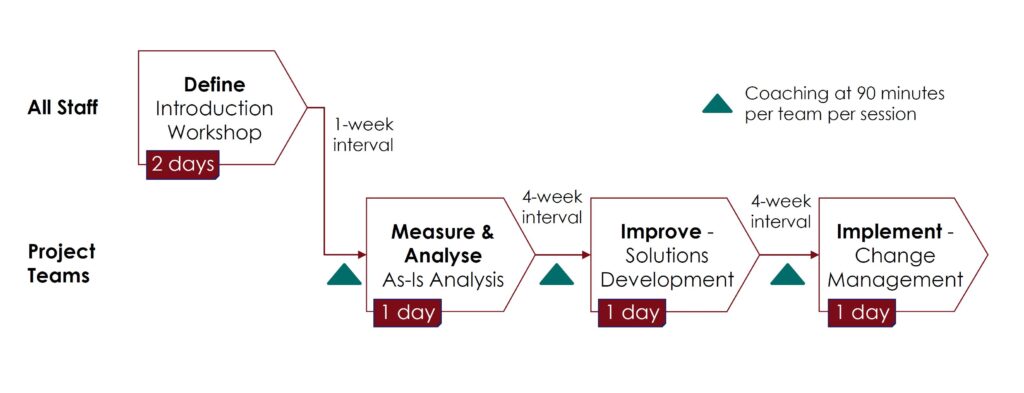
The focus of our LIT is on application and producing measurable process improvements whilst instilling the mindset in people that they “can innovate”. Therefore, it is powered by action-learning and includes 90min of project specific coaching per team after each training session.
Lean Innovation Training Alive
Our Lean Innovation Training (LIT) has been developed for an organisation who had exactly the same worries regarding LSS as many others. They mentioned:
- “LSS takes too long for solving problems. We cannot wait for six months before we have a solution to problems that arise today.”
- “LSS teaches tools we never need due to the character of their problems.” In particular, they raised concerns that the usual Six Sigma statistics were not needed when their issues resulted from long turn-around-time for processes.
- “LSS Green Belts need to receive about ten days of training and some coaching in order to deliver results and, hence, qualify for a certificate. This is a burden we cannot handle.” This seems to be a worry for many organisations.
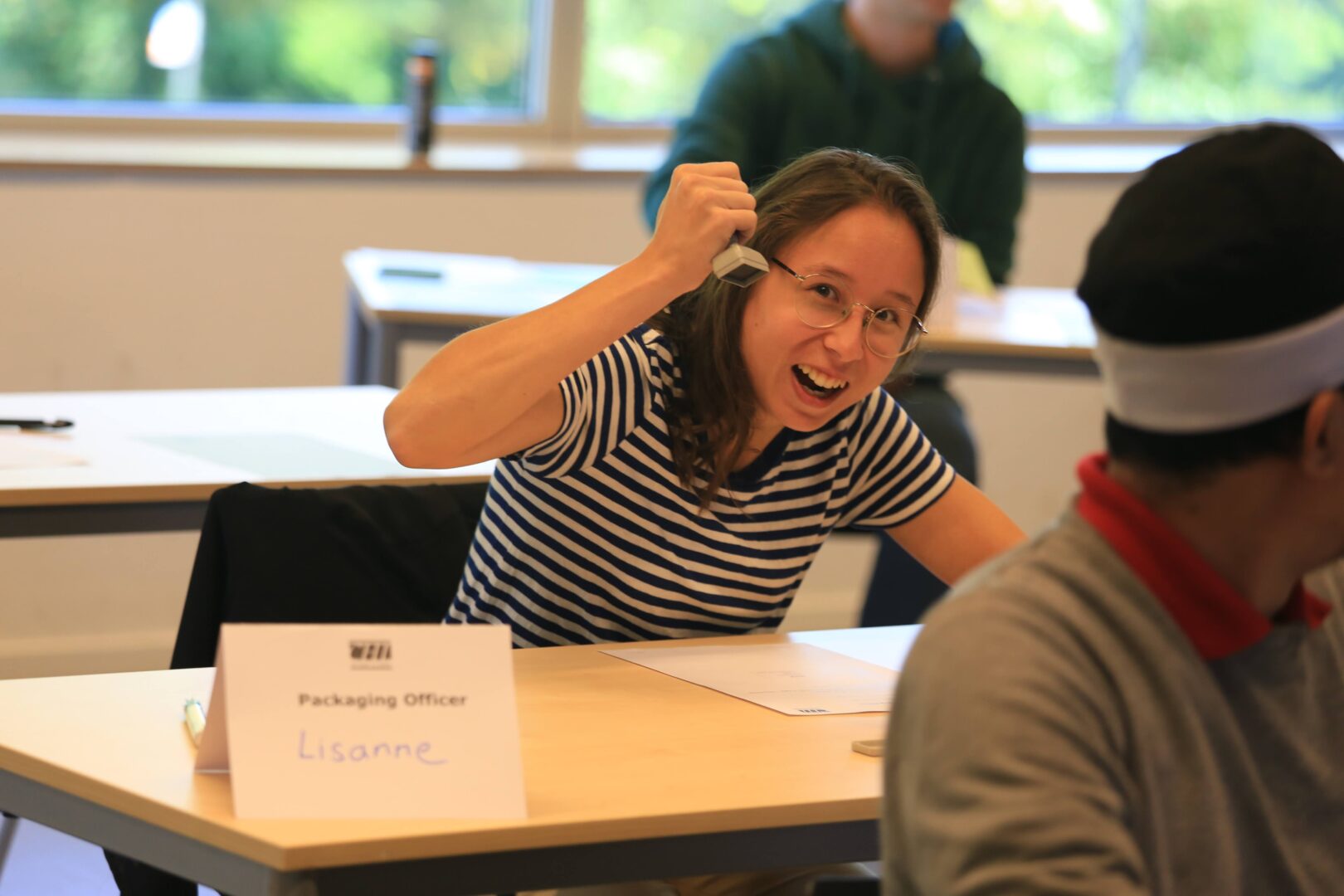
As a result, we designed a training that was using the powerful DMAIC roadmap to keep the proven rigour. At the same time, we reduced the number of training days to five. We achieved this by removing some tools that were obviously not of help for the projects in scope. Whilst we kept the waste-reducing Lean tools, we removed some variation-analysing LSS statistics.
Conclusion
Secondly, our Lean Innovation Training supports leaders and managers to promote innovative behaviours amongst employees and drive an innovation culture in their organisation.
- All Posts
- Innovation
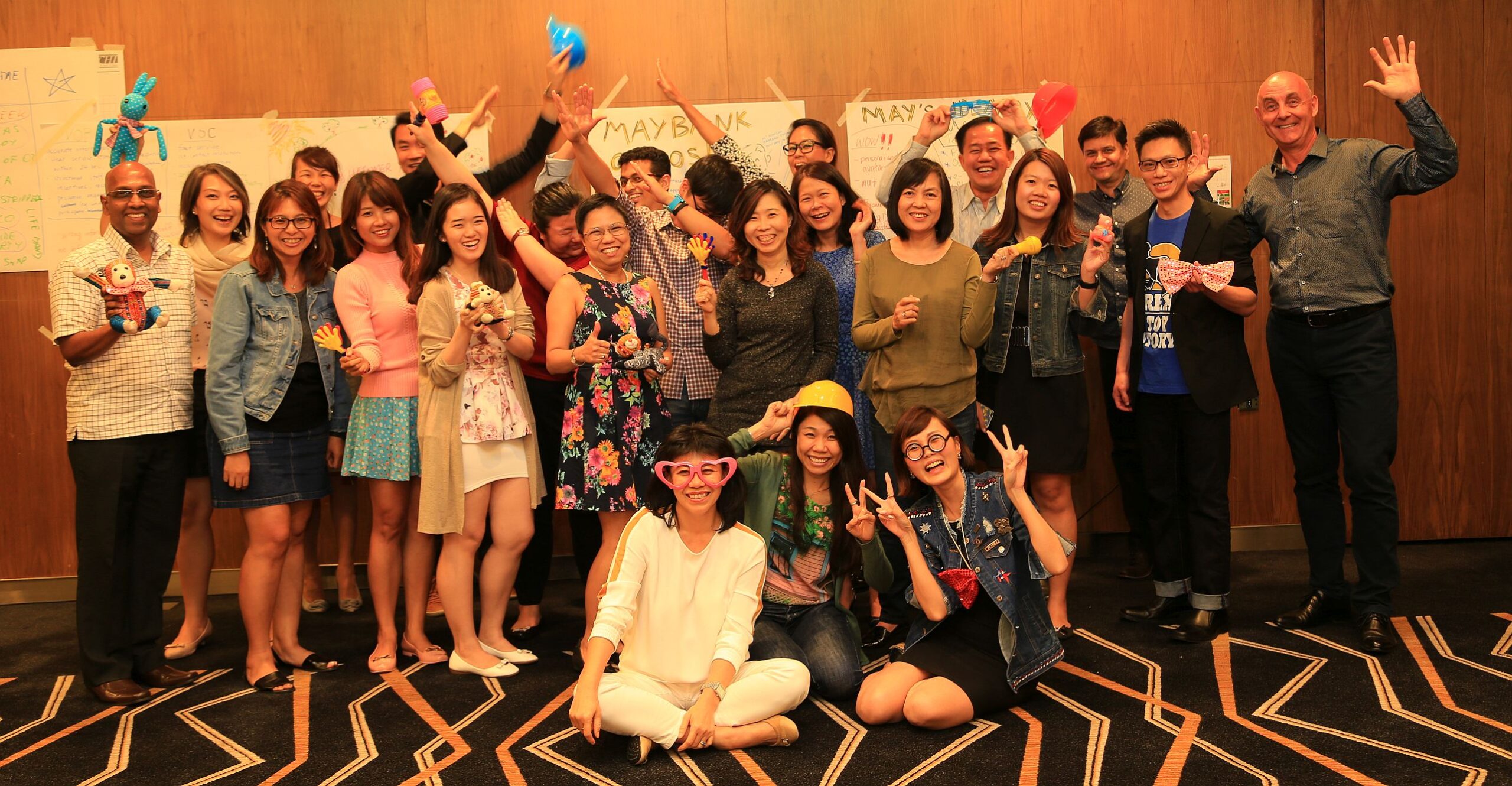
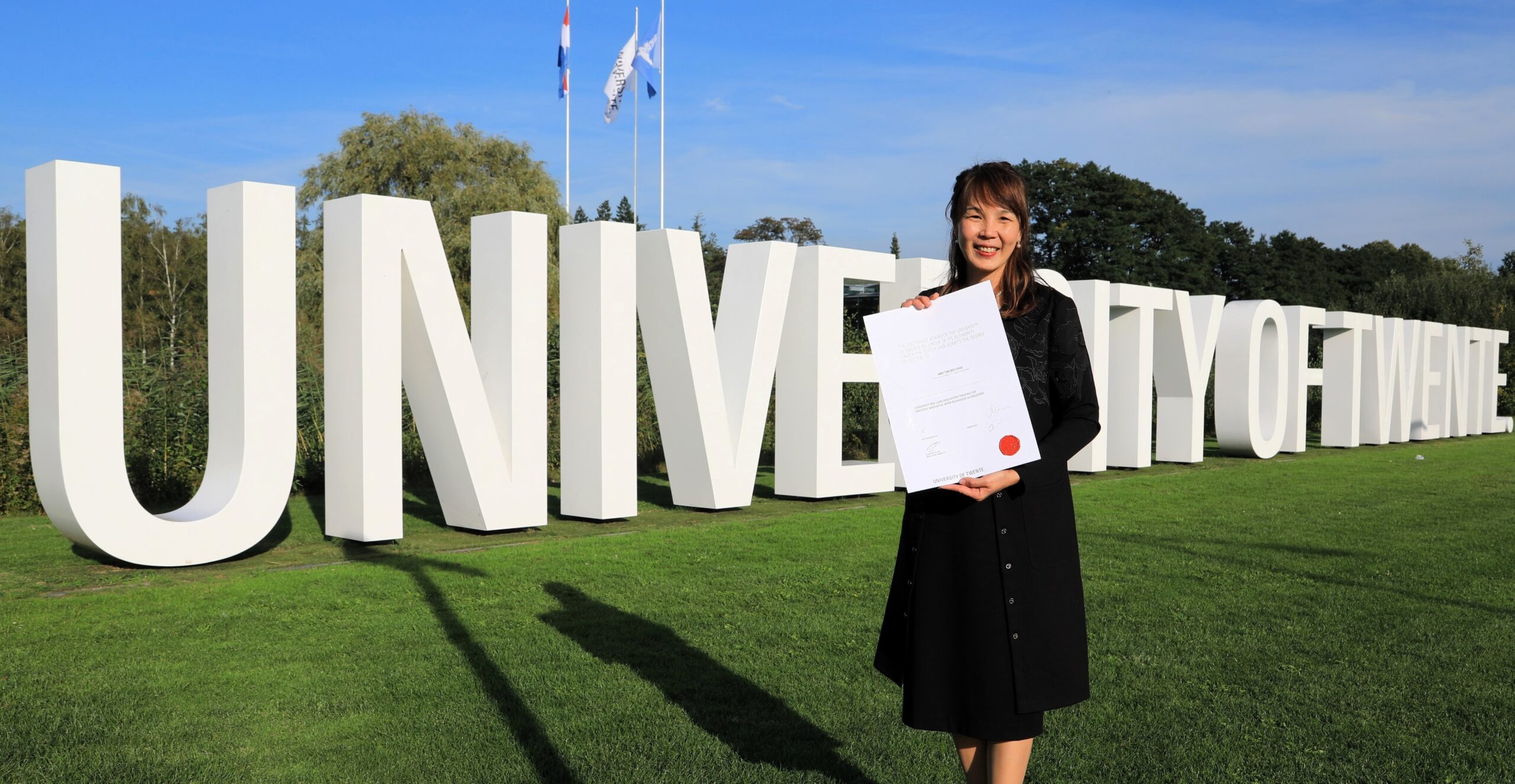
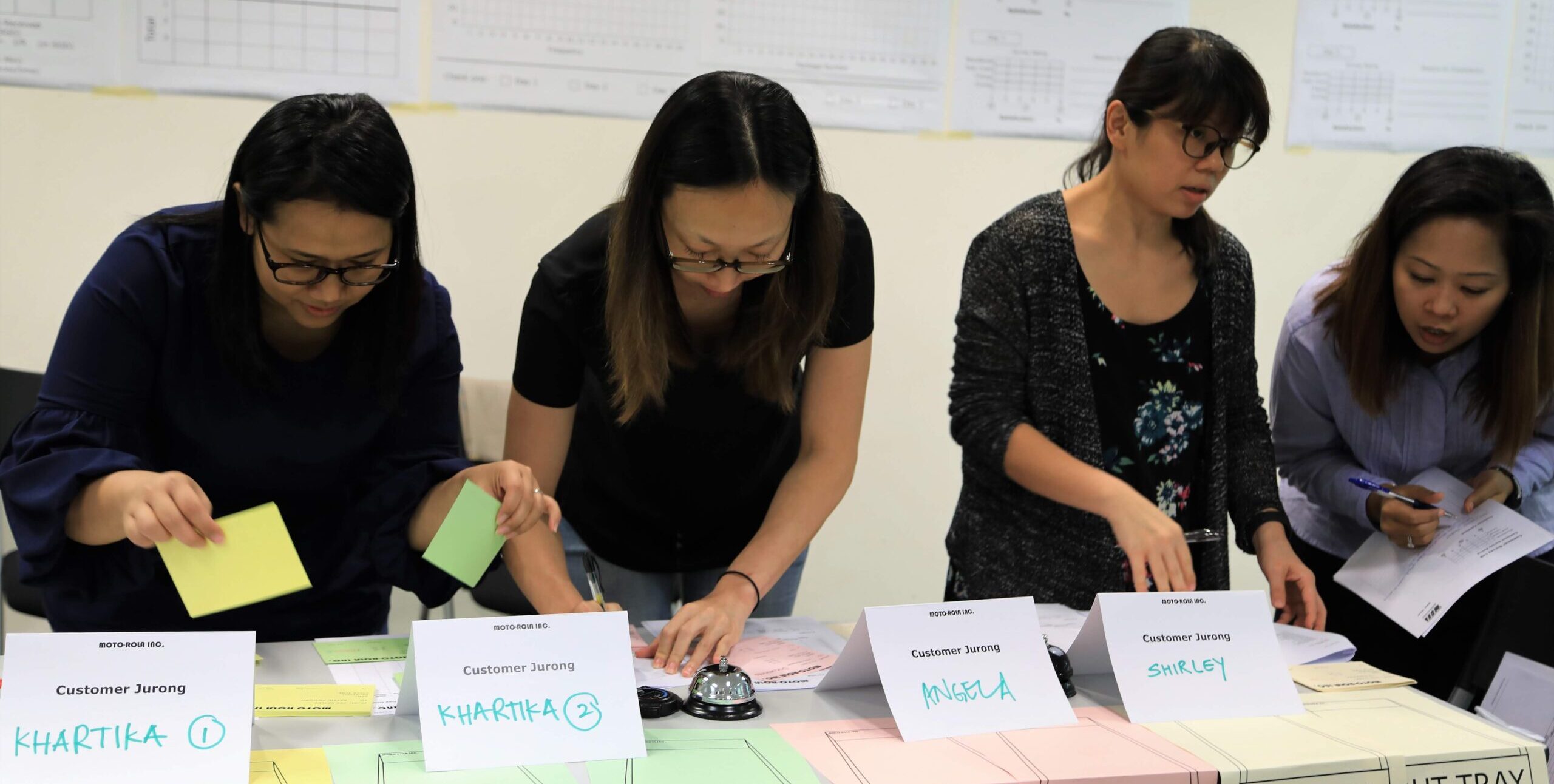
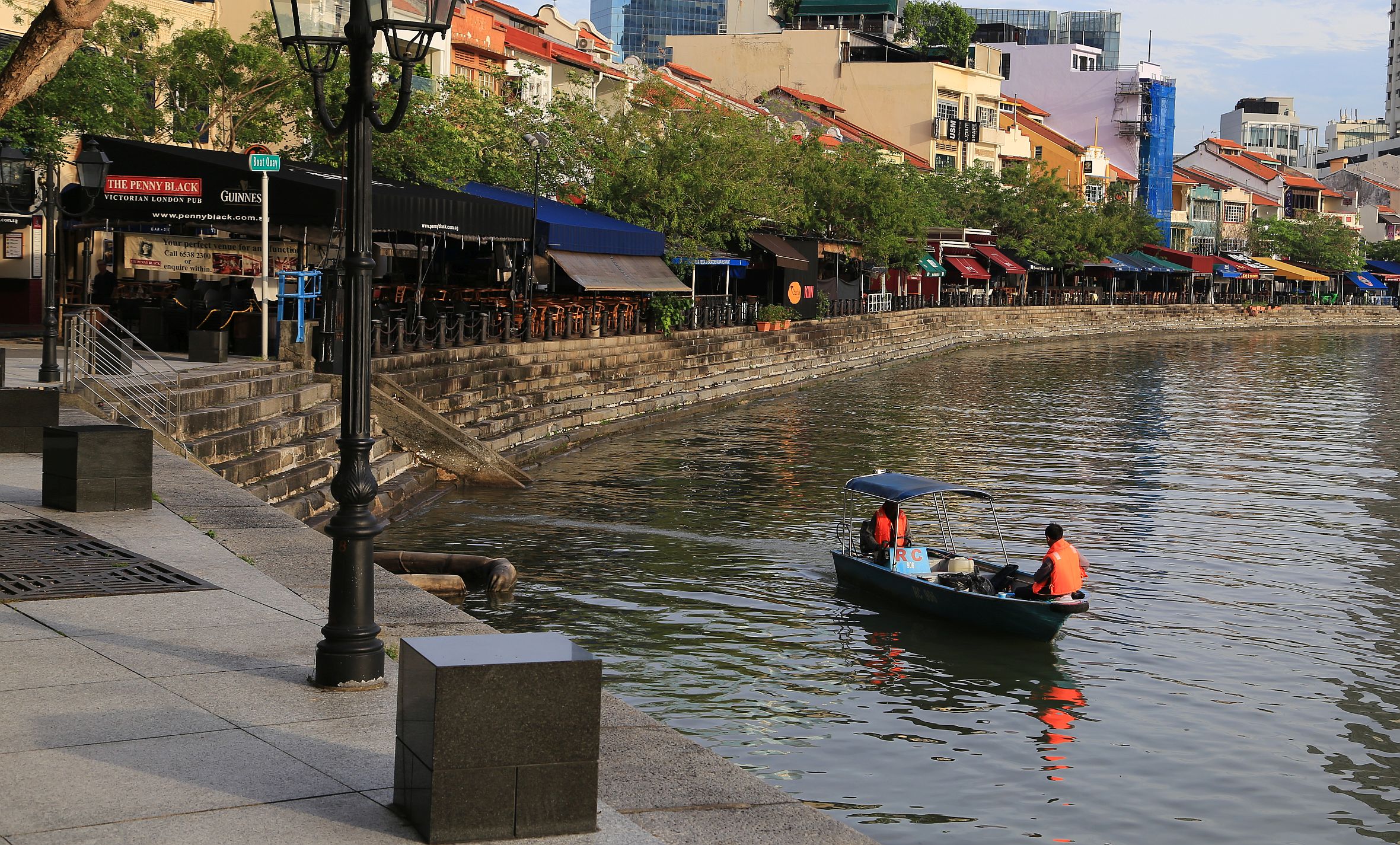
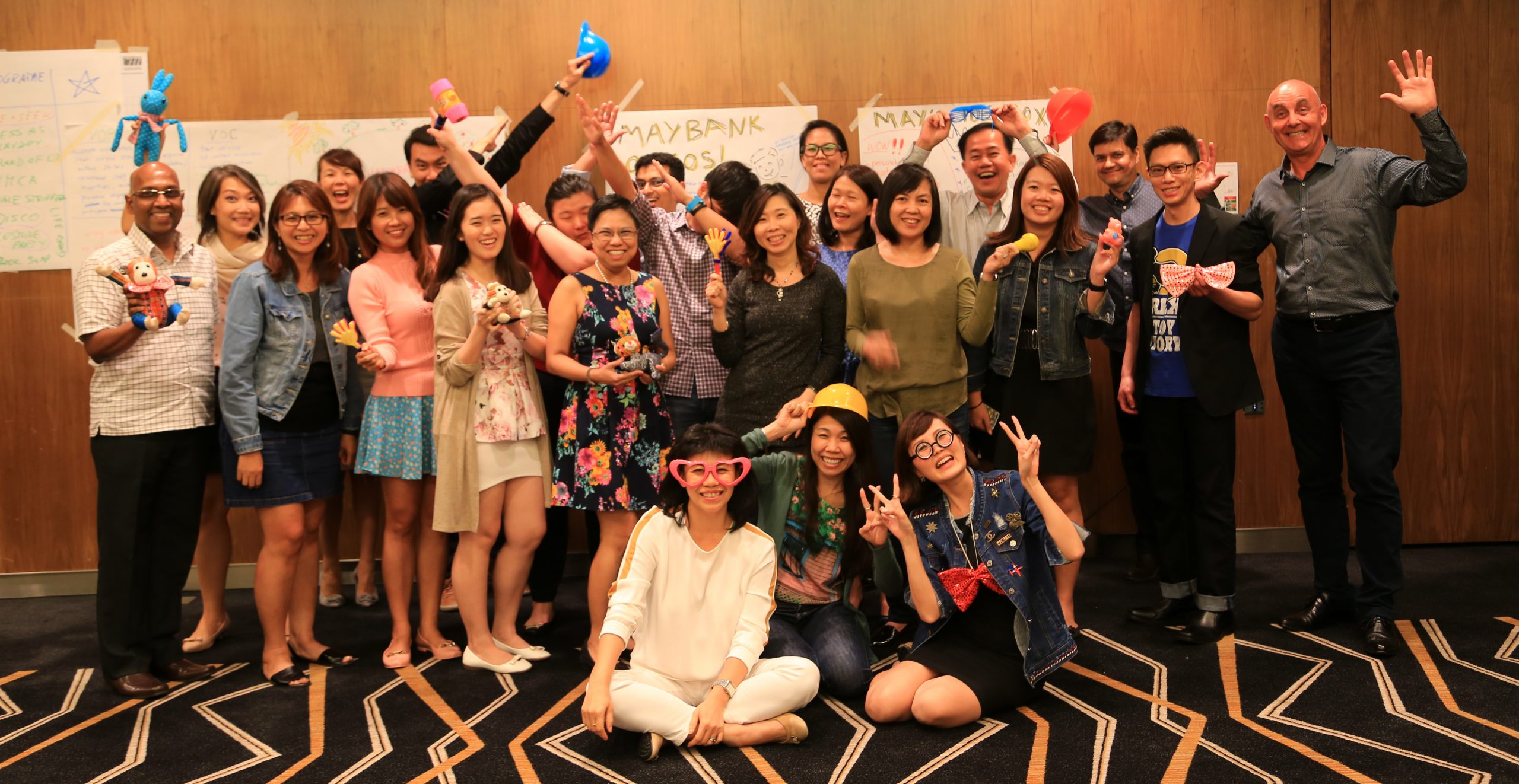
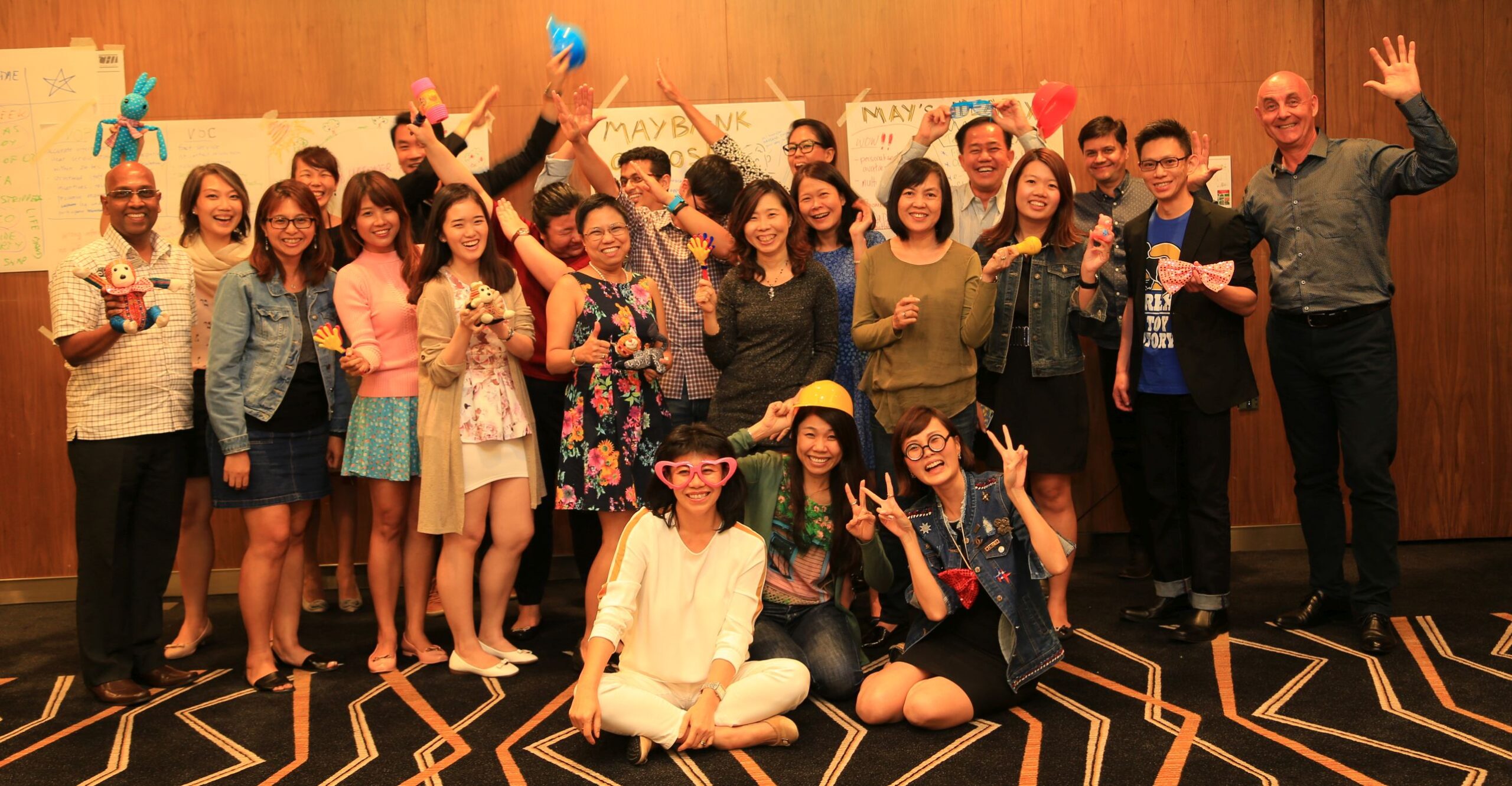