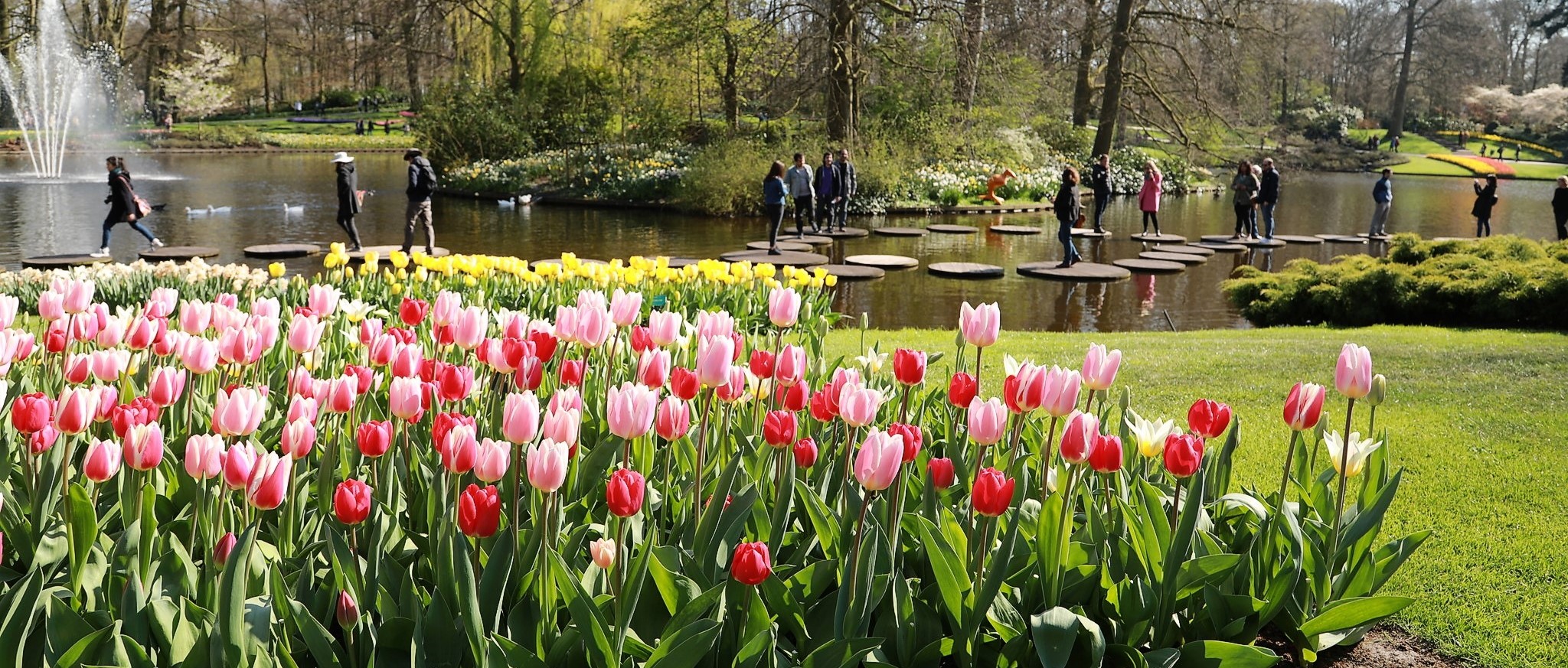
- +65 61000 263
- Contact@COE-Partners.com
- Newsletter
Manufacturing: Lack of Skills: If workers are not adequately trained or skilled, it can lead to production errors, inefficient methods, and increased defects. For instance, an operator who lacks training may not use machines properly, resulting in wasted materials and time.
Service: Underutilisation of Skills: Employees may have skills that are not being effectively used in their current roles (e.g., a customer service representative with advanced problem-solving skills may only be handling basic inquiries, leading to wasted potential and missed opportunities for better customer experiences. This may also result in demotivation and attrition).
Copyright © 2025 by COE Pte Ltd. All Rights Reserved.